New Coroner Facility - Sustainable Building and Energy Usage
Prolonged health for employees, operational functionality, and longevity. These were the underlying goals established during the first owner/architect workshop for the New Will Coroner’s facility. The need for this project traced back over a decade, so it was crucial to get all the details right this time around.
The 11,460 SF building footprint was divided into three main functions: Office, Autopsy Suite, and Sallyport (for ingress/egress, building systems, and storage). Once the adjacencies were resolved in a manner that served the staff and fit site parameters, it was time to step back and focus on the goals determined in the early workshops.
Energy Modeling Tools
Cove Tool is a sustainable building design and energy modeling software that we implemented early on to help maximize natural light infiltration. There are often misconceptions that too many windows, or too much natural light, can be a detriment to building performance and thermal comfort for those working inside. While this can be true in many cases, there are more important factors to analyze before reducing window quantities. The first is the building’s orientation as it relates to geographical location. Once this is determined, window placement along each elevation becomes very crucial. In our case, the Office function faced North, meaning we could place a good amount of glazing along that elevation without introducing too much glare. We also knew that we would be installing high performance insulating glass units with a Low-E coating throughout the facility to deter excessive amounts of solar heat gain.
There were two key tests from Cove Tool that helped justify our fenestration design. The Annual Sunlight Exposure (ASE) Test identified two small zones along the East & West Elevations that had potential for higher glare readings. Manually operable window shades were provided in each location so employees could adjust as needed. The Basic Daylight Autonomy (sDA) Test determines if rooms within a building are meeting minimum daylight illuminance levels for working hours throughout a calendar year. We passed the test in all areas of the building that would be regularly occupied by employees, even the two autopsy labs. Providing an abundance of daylight and sightlines to the outdoors vastly improves working environments. To accentuate this in the new facility, the five private offices placed along exterior walls were equipped with wall to wall & floor to ceiling interior glazing. This allows daylight to pierce deep into the more centrally located open office area.
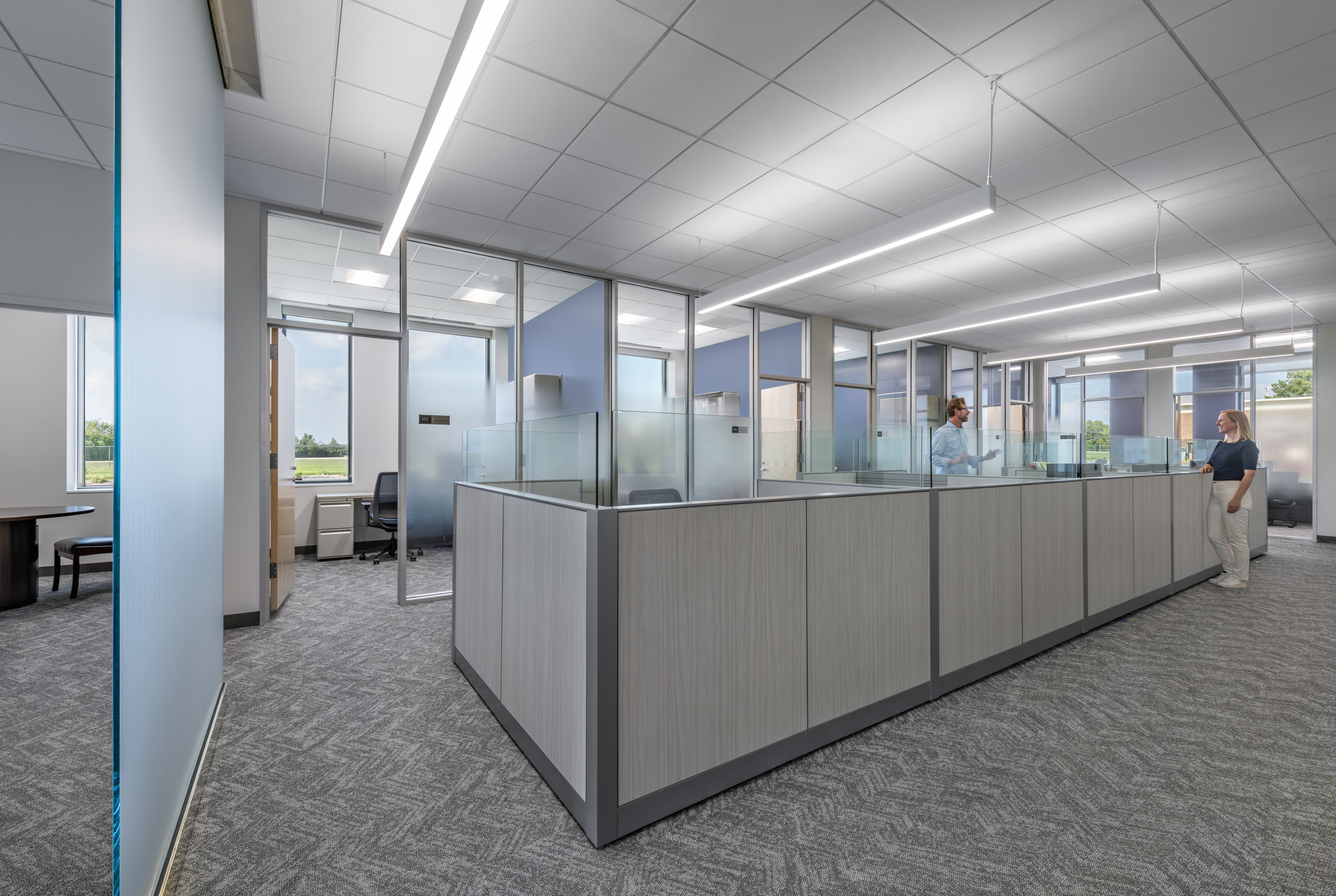
Building Material Considerations
Materiality is always important when discussing sustainability. The variegated and monolithic brick expressions that wrap most of the facility provide a durable finish to protect the fully continuous foil-faced wall insulation that that is situated outboard of the exterior sheathing and fluid applied air barrier. The brick wall system ties into the Metal Composite Rainscreen Panels that descend from the roof to grade and articulate the main building entry. The continuity of the air barrier from exterior wall base up to the roof parapet and overlapping roof membrane help to mitigate air leakage and thermal conductivity that can result in condensation within the wall, and tends to accelerate the corrosion of internal building materials.
Once the design for the building envelope was completed, we had to focus on one of the more complicated interior spaces. The Coroner’s staff needed a large area (23’ wide x 53’ long) for a walk-in freezer/cooler enclosure with direct adjacency to the autopsy labs. This project fell under the 2018 International Energy Conservation Code which provided strict thermal parameters for “cold rooms” (Walls R-25 Min., Doors R-32 Min., and Ceilings R-28 Min.). These components all came from a sole sourced equipment manufacturer, so we placed the Energy Code parameters on the drawings and in the project specifications to ensure compliance. The Energy Code also requires walk-in freezer floors to have a minimum thermal resistance of R-28. This is where the technical detailing of the space became very important. The concrete slab below the cold rooms had to be thermally isolated from the slab serving the rest of the building via floor joints with compressible filler or wood. Moreover, there needed to be a thermal break between the cooler floor and freezer floor, due to the R-28 requirement for the latter. If you took a knife and cut a cross-section through the freezer floor the makeup from top to bottom would be as follows: 5” concrete topping slab, felt sheet layer, 4” rigid insulation, vapor barrier, 5” slab on grade - picture a 5-sided metal box with a dividing partition in the middle placed on top of the isolated slabs, and you have something very similar to our configuration sans the cooling equipment.
Mechanical and Electrical Considerations
Heightened performance requirements in the labs made it difficult to out exceed Energy Code minimums regarding the Mechanical and Electrical scope. However, the integration of occupancy and daylight sensors was instrumental in contributing to energy conservation on this project. The occupancy sensors ensure the lights are activated only when needed assuring energy savings and lifespan of light fixtures. The daylight sensors adjust artificial lighting levels based on available daylight, maintaining an optimal illumination balance throughout the day. This reduces electricity consumption and fosters a more comfortable, well-lit environment. The Autopsy suite has a fully automated HVAC system, and the ancillary spaces are designed to achieve optimal comfort while maintaining required lab ventilation. The laboratory grade exhaust works in conjunction with zone airflow systems. This keeps the exhaust operating as efficient as possible while all zone level comfort and pressure levels are tightly maintained. The two autopsy labs also feature Demand Control Ventilation to allow for reduction in airflow when the suites are not in use, which in turn helps to conserve fan and electric energy usage.
Health and Wellness
Wright and Company strives for all their projects to be sustainable, and that goes beyond building systems and enclosure materials - employee health and prosperity are of equal importance. We discussed design strategies that enabled an abundance of natural daylighting in all the occupied rooms. In supplement, a calm and soft interior color palette was selected to compliment the ambient lighting strategy. Accents of subdued blue were strategically placed throughout the facility. Psychological studies tell us that blue is favored by most and typically evokes a feeling of calmness and relaxation.
The Coroner and her staff also informed us of the communal traditions they would like to start in the new building, such as having a place to cook and eat dinner together when working through holidays, or comfortable places to sit down and unwind during a lunch break. To provide this hybrid break & living area, we pulled the volume as far away from the office and lab areas as possible. The transition corridor was then painted with our accent blue on one wall and organic wall covering on the opposite, which created a buffer between the work and repose areas. The open entry to the break & living area is marked by the transition from carpet tile to warm wood look LVT floor planks & the calming felt lighting pendants. From here, the users have access to the full kitchenette niche recessed into the wall to create more circulation space – or the sofa and tv at the far end of the room that resonates a residential ambiance. When the weather is nice, employees can bring their lunches to the outdoor patio with direct access from the break area.
The Coroner is now equipped with a state of the art facility that can keep up with the administrative and forensic analysis demands of Will County for the foreseeable future - a home that will allow her staff to accomplish tasks at a high level while providing them with a comfortable space to decompress.
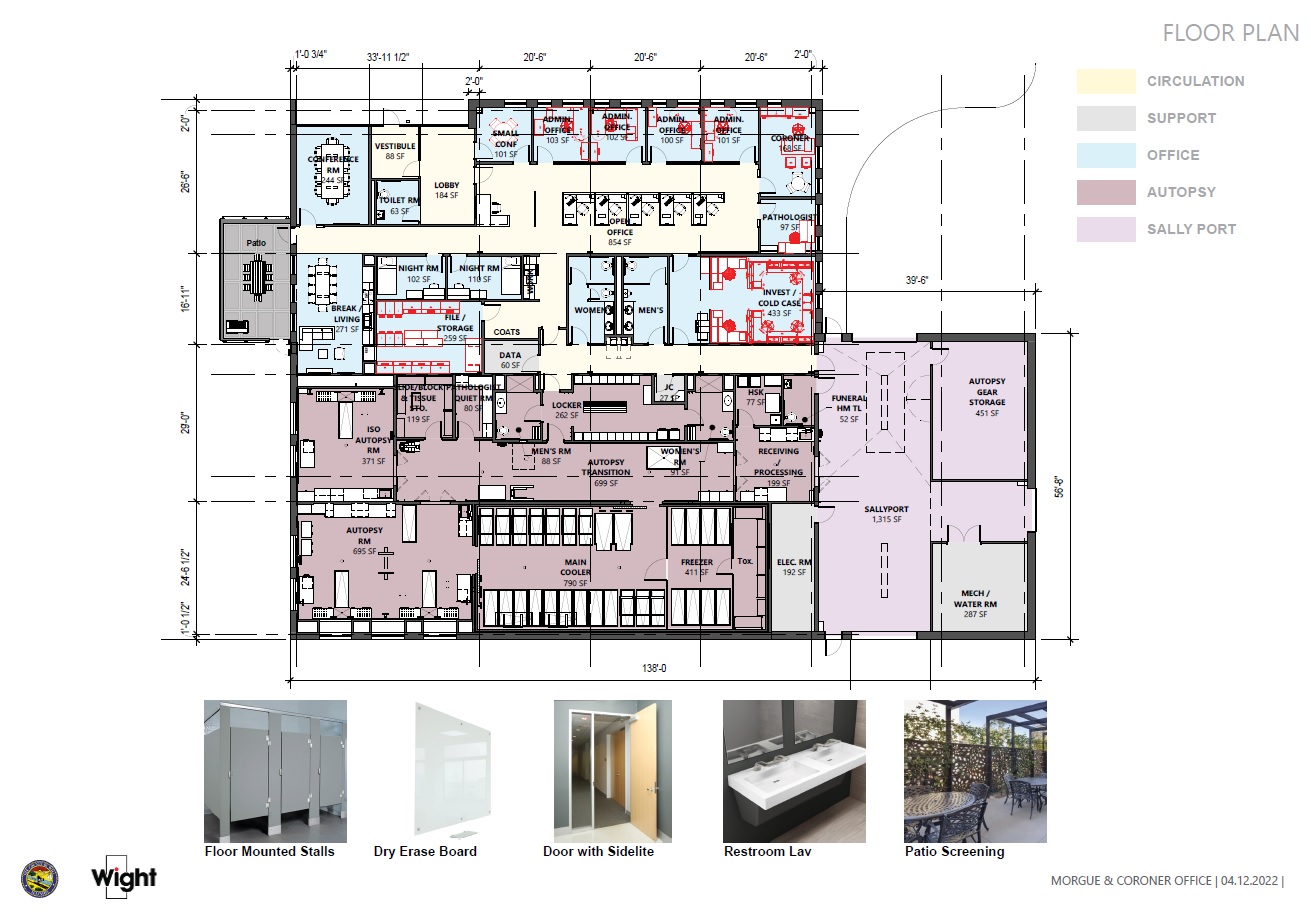
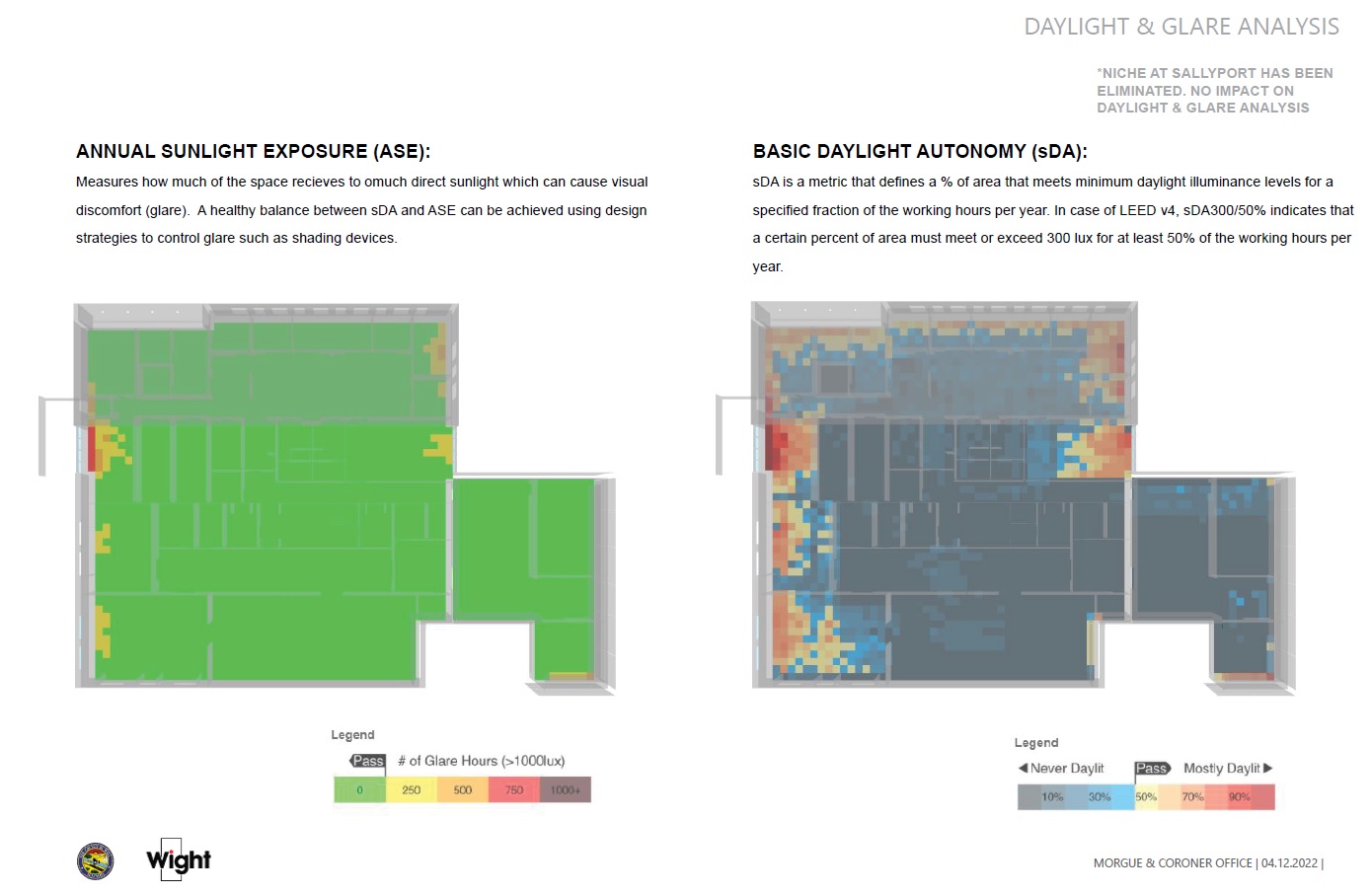
Information provided by the Architect of Record
Wight & Company
2500 North Frontage Road
Darien, IL 60561
630.969.7000 | d 630.739.7233
www.wightco.com
Photography: Connor Steinkamp Photography
Last updated 10/20/23